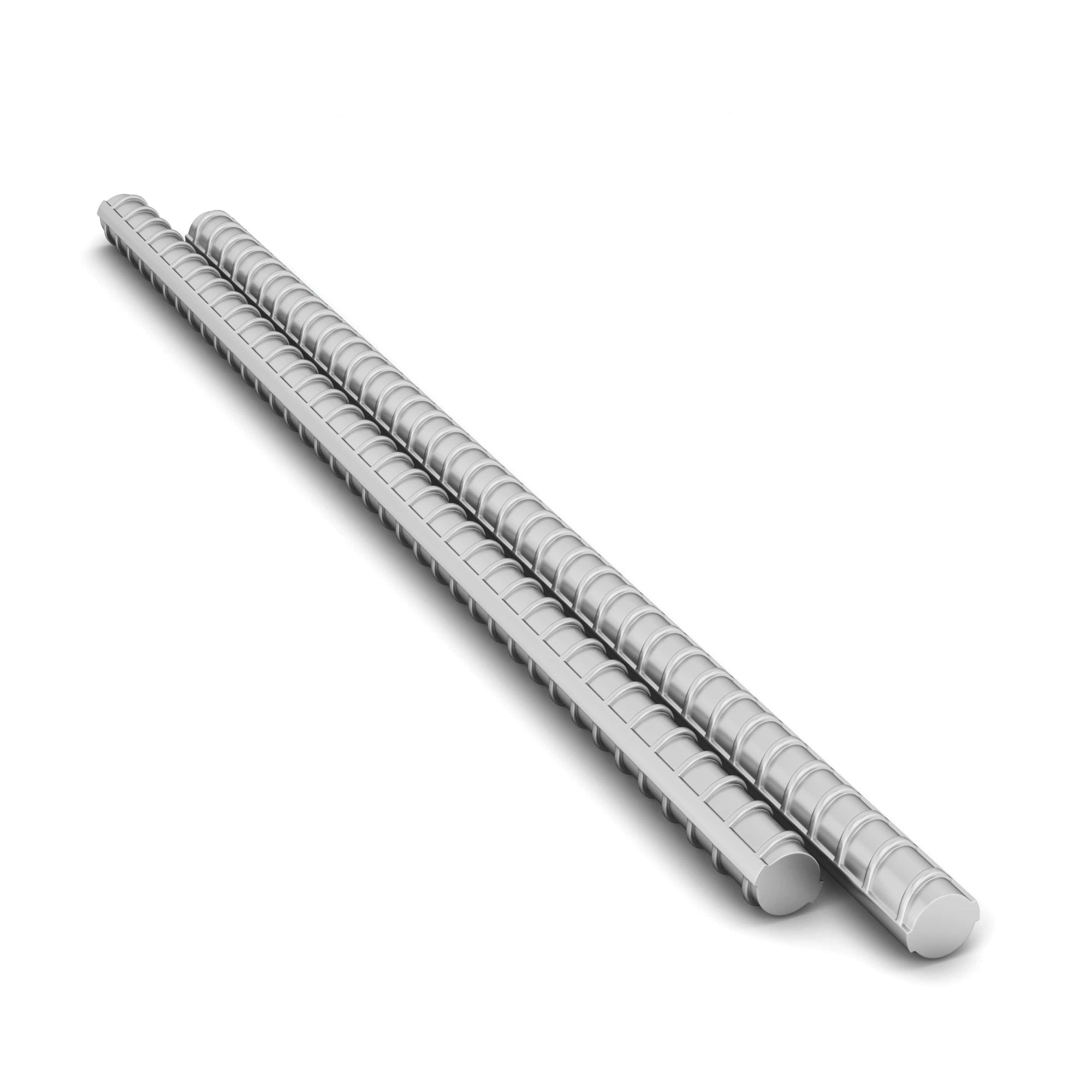
Trustpilot
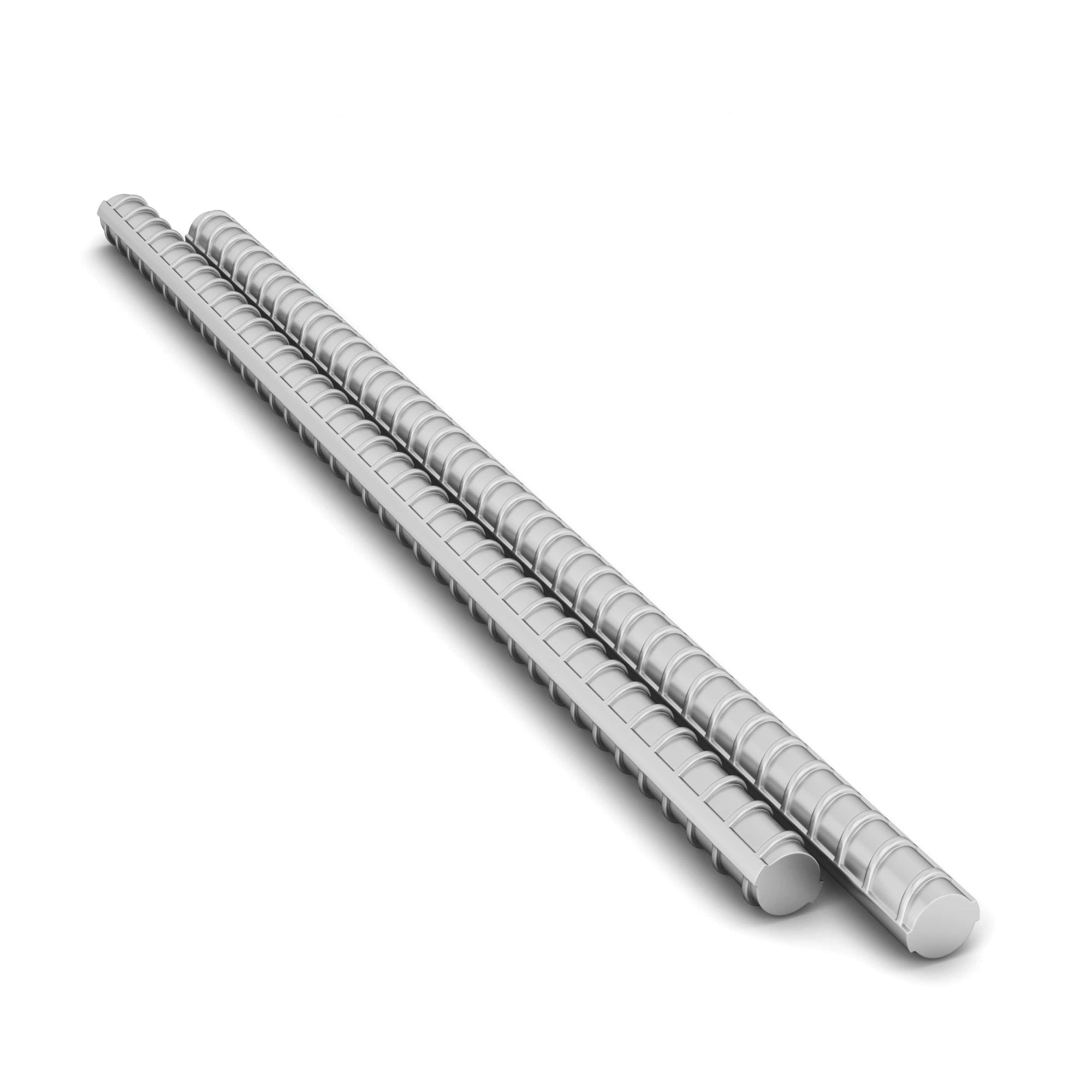
Trustpilot
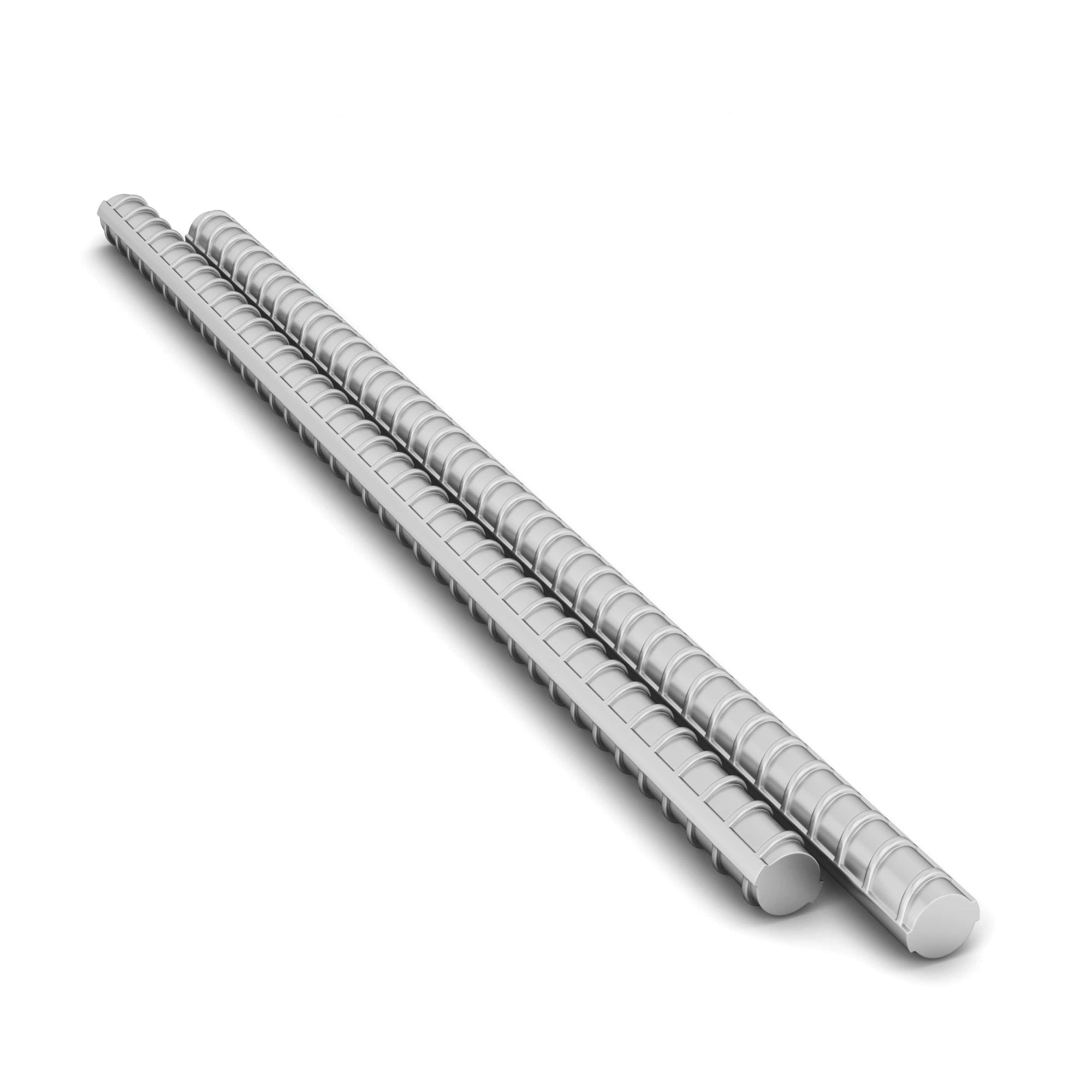
Trustpilot
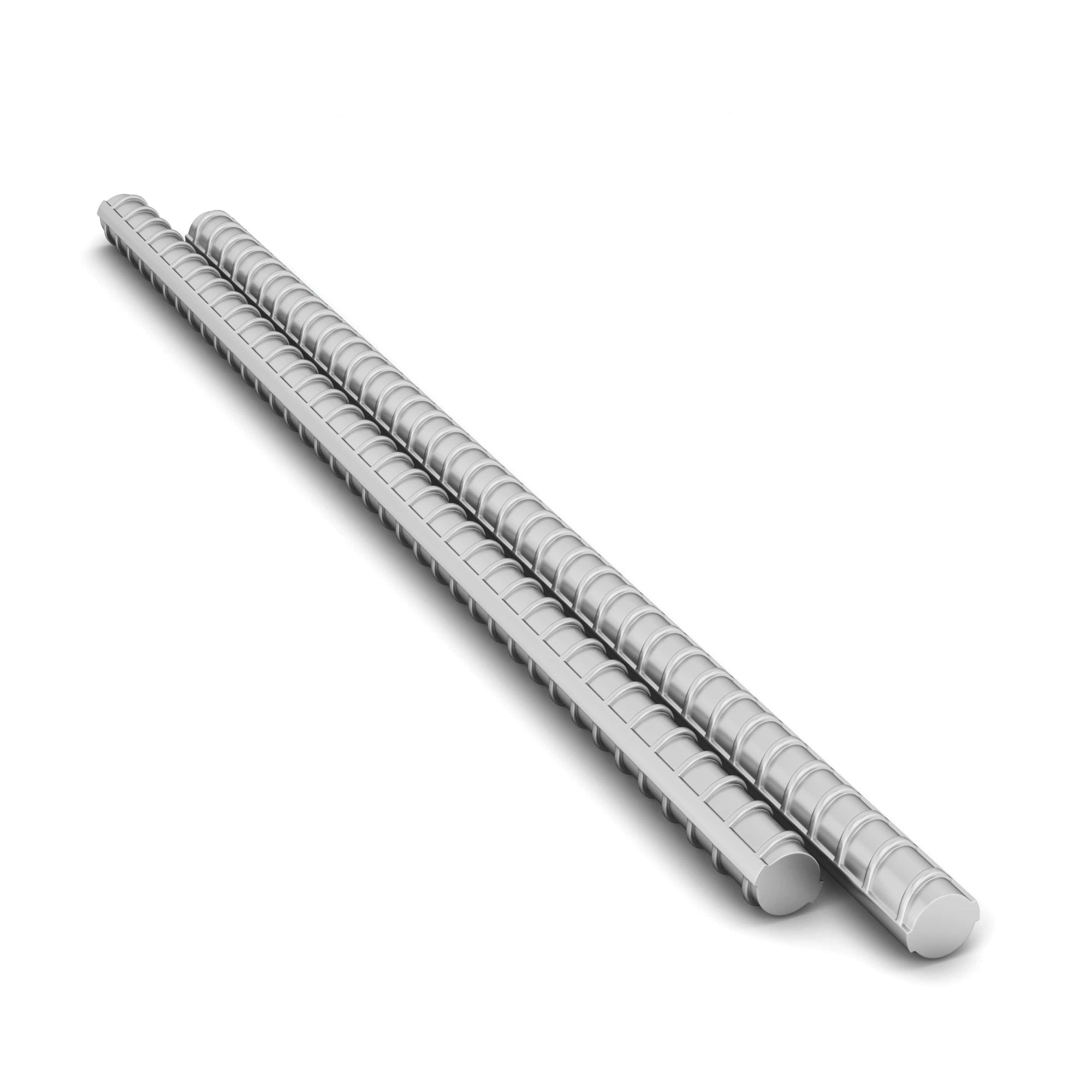
Trustpilot
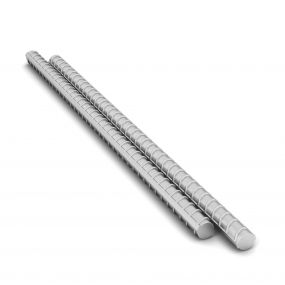
Thicknesses: 10mm, 12mm, 16mm, 20mm
Spring Sale - 5% OFF orders £50+ -
Reinforcement bar, more commonly known as rebar, is a ribbed steel bar that interlocks with concrete to provide tensile strength while remaining flexible to resist cracks. This makes it essential for strengthening concrete structures, with applications ranging from foundations, columns, slabs, walls, bridges and tunnels. Our stock includes a wide range of rebar sizes from 10mm diameter up to 20mm, in standard lengths or custom cut-to-length. Our rebar inventory comes bundled or loose depending on preference.
Trustpilot
Trustpilot
Trustpilot
Trustpilot
Thicknesses: 10mm, 12mm, 16mm, 20mm
Handheld manual shears or electric shears can cut small-diameter rebar, while larger diameters are best managed with either an abrasive chop saw or a horizontal bandsaw. Angle grinders using abrasive discs may also be used, although they present a higher fire risk. For very large rebar, thermal cutting with plasma torches represents the fastest option, albeit requiring greater equipment expenditure initially.
Rebar can be bent manually for smaller diameters using knee benders, lever benders or pin benders secured in a vice, allowing custom shapes to be formed on-site prior to concrete pouring. For larger diameter rebar and complex bending requirements, hydraulic or electric-powered rebar benders are available that use couplers and dies to bend bars up to 60mm into precise shapes for prefabrication. Care must be taken to avoid overstressing the steel during bending which can lead to fracture.
Rebar can be tied together using annealed iron wire that is wrapped tightly around intersecting bars to create a rigid mat or cage shape prior to pouring concrete. Alternatives to wire tying include plastic and metal rebar ties, or tack welding the connections.
Welding rebar requires care to avoid excess splatter, cracking, or reduced strength in the heat-affected zone around the weld. Smaller diameter rebar can be welded using basic MMA/stick or MIG techniques with low hydrogen E7018 or rutile flux-cored consumables, while larger diameters will benefit from preheating first to 150-200°C to reduce residual stresses. Good joint preparation through bevelling or chamfering the ends, in addition to allowing bars to cool slowly after welding, will help maintain strength.
Verified
Verified
Verified
Verified
Verified
Verified
Verified
Verified
Verified
Verified
Verified
Verified
Verified
Verified
Verified
Verified
Verified
Verified
Verified
Verified
Verified
Verified
Verified
Verified
Verified
Verified
Verified
Verified
Verified
Verified
Verified
Verified
Verified
Verified
Verified
Verified
Verified
Verified
Verified
Verified