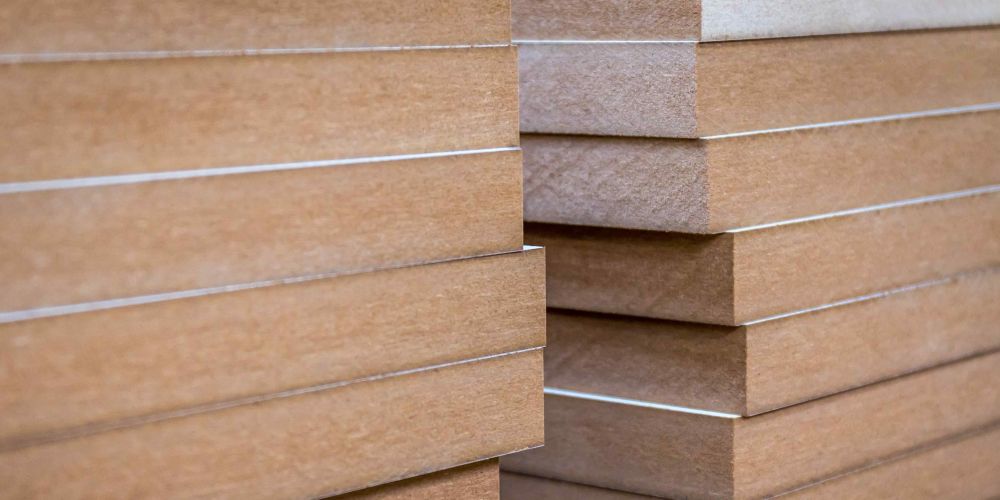
If you've ever purchased flat-pack furniture, worked on a home renovation, or had new kitchen cabinets installed, chances are you've encountered MDF. This engineered wood product has become an integral part of modern furniture and construction. But what exactly is MDF, and why is it so widely used? Let's explore the properties and applications of this versatile material.
What is MDF Made Of?
MDF stands for "medium-density fiberboard." Despite its name, it doesn't actually contain any wood fiber. Instead, MDF is manufactured from recycled wood particles, like sawdust or wood chips, that are blended with wax and resin binders.
The manufacturing process begins by defibrating the wood particles into smaller wood fibers. These fibers are then combined with a wax (to enhance moisture resistance) and a resin binder, typically urea-formaldehyde. This mixture is formed into a mat and pressed under intense heat and pressure, causing the resin to cure and bind the wood fibers together. The result is a flat, dense panel with a remarkably smooth and uniform surface.
Properties of MDF
One of the standout features of MDF is its density. It's denser than particleboard but lighter than conventional wood panels, which contributes to its impressive strength and stiffness, making it suitable for load-bearing applications like shelving and cabinetry.
The uniform composition and smooth surface of MDF make it easier to finish than natural wood. It doesn't have knots, grooves, or other imperfections found in solid wood, allowing for a consistently flawless paint or laminate finish.
While not waterproof, MDF does offer better moisture resistance than standard particleboard thanks to the wax additives used in its production. However, it's still important to protect it from excessive moisture to prevent swelling or delamination.
Perhaps the biggest advantage of MDF is its workability. It cuts cleanly and takes screws, nails, and other hardware with ease, making it a dream material for woodworkers, DIYers, and flat-pack furniture manufacturers.
Types of MDF
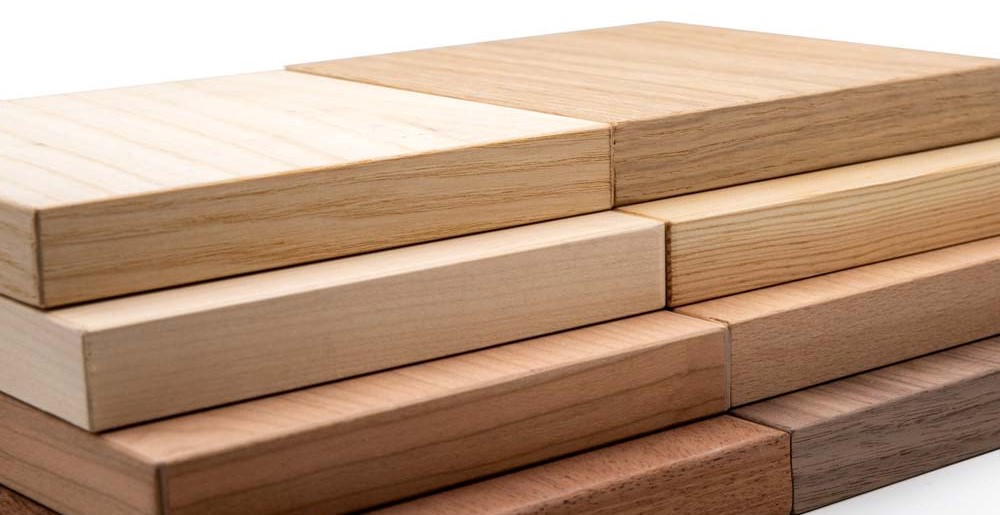
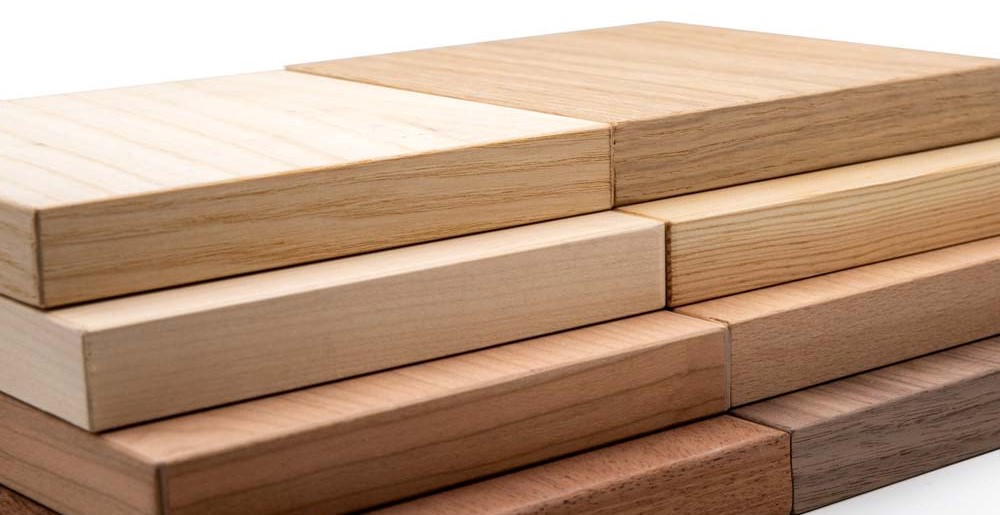
While MDF generally refers to standard medium-density fiberboard, there are several variations available to suit different application needs:
- Standard MDF: The most common type, with a density ranging from 600-800 kg/m³. It offers a good balance of strength, affordability, and workability for general-purpose use.
- Moisture-Resistant MDF: Also known as MRMDF, this type features increased moisture resistance through the addition of resins or wax additives, making it better suited for areas with higher humidity or moisture exposure.
- Fire Retardant MDF: Treated with fire-resistant chemicals during manufacturing, this type of MDF meets fire safety standards for building materials and construction applications.
- High-Density Fiberboard (HDF): With a density exceeding 800 kg/m³, HDF is exceptionally hard and durable, making it ideal for heavy-duty applications like flooring, stair treads, and worktops.
- Ultra-Light MDF: On the other end of the spectrum, ultra-light MDF has a density below 500 kg/m³, offering superior insulation properties and easy workability for applications like door cores and sound-absorbing panels.
- Veneered MDF: These panels have a thin wood veneer laminated onto one or both sides, providing the aesthetic of real wood while benefiting from MDF's stability and smooth core.
- Melamine MDF: Featuring a melamine resin surface on one or both sides, these panels have enhanced moisture, stain, and scratch resistance compared to raw MDF.
For a more comprehensive guide on the different types of MDF and their specific properties, check out our in-depth MDF Types & Their Uses article.
What are the Advantages of MDF?
Cost-Effectiveness
One of the primary reasons for MDF's widespread adoption is its cost-effectiveness. As it's made from recycled wood fibers and sawmill waste, it's more affordable than solid wood panels while still offering excellent performance.
Consistent Quality
With its manufactured, uniform composition, MDF provides a consistent quality that can be difficult to achieve with natural wood products. This consistency is crucial for mass-production applications where dimensional accuracy and a smooth finish are essential.
Versatility
MDF can be used in a wide range of applications, from furniture and cabinetry to construction, flooring, and even signage. Its strength, workability, and smooth surface make it suitable for various projects.
Environmental Benefits
While not a purely sustainable product due to the resin binders used, MDF does offer environmental advantages over solid wood panels by utilising recycled wood fibres and sawmill waste. reducing the need for solid timber.
Limitations and Concerns
While MDF offers many advantages, it's not without its limitations and concerns:
Moisture Resistance
Although MDF has better moisture resistance than standard particleboard, it's still susceptible to swelling and delamination if exposed to excessive moisture or high-humidity environments.
Edge Swelling
The edges of MDF panels are particularly vulnerable to moisture absorption, which can cause unsightly swelling and delamination.
Formaldehyde Emissions
The resin binders used in MDF can release formaldehyde, a volatile organic compound (VOC) that may cause health concerns if present in high concentrations. However, all of our MDF products comply with strict formaldehyde emission standards.
Dust Hazard
The resin binders used in MDF can release formaldehyde, a volatile organic compound (VOC) that may cause health concerns if present in high concentrations. However, all of our MDF products comply with strict formaldehyde emission standards.
What is MDF Used For?
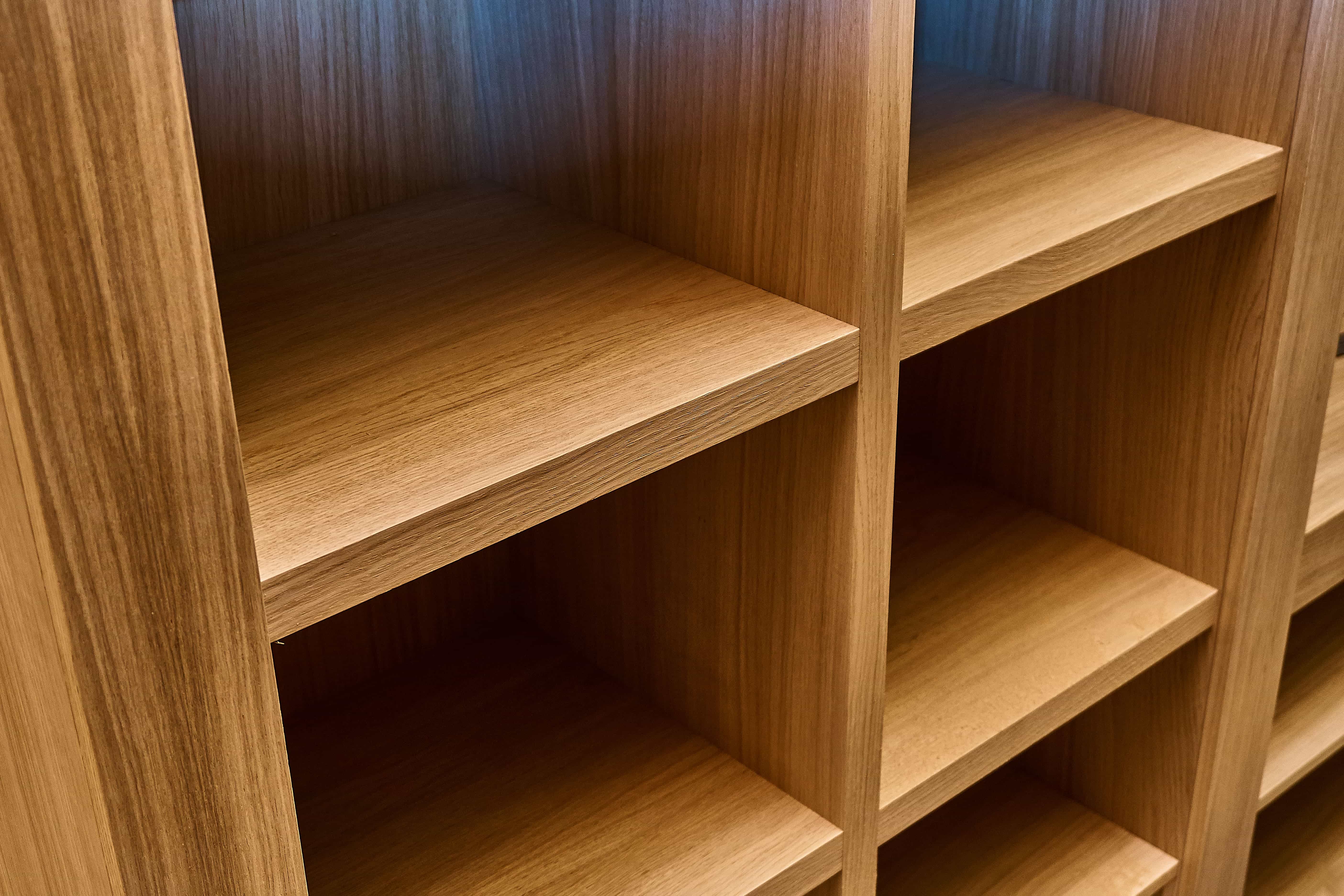
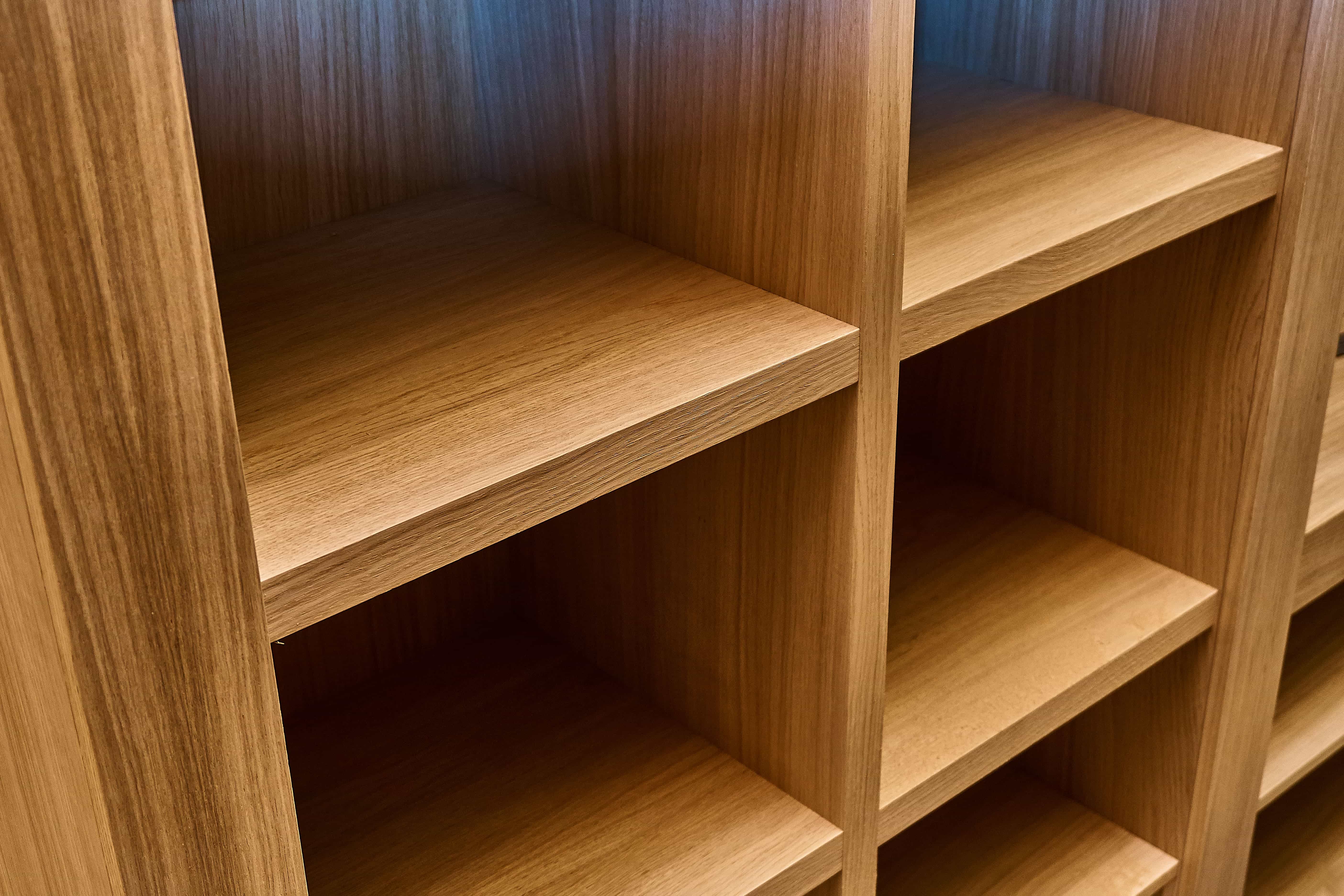
Furniture
MDF is a popular material for flat-pack and ready-to-assemble furniture, such as cabinets, shelving units, desks, and more. Its strength and smooth surface make it ideal for furniture components like cabinet doors, drawers, and desk table tops.
Construction
In the construction industry, MDF is used for interior trim, mouldings, doors, and even structural components like floor joists and load-bearing beams (in engineered wood products like I-joists).
Flooring
MDF is commonly used as an underlayment for laminate and hardwood flooring installations. It can also be the core material in some types of laminate flooring planks.
Other Uses
The versatility of MDF extends beyond furniture and construction. It's also used for signage, toys, packaging, and various DIY projects where a smooth, uniform surface is desired.
How Does MDF Compare to Other Sheet Materials?
While MDF shares some similarities with other wood-based products like plywood, particleboard, and MFC (moisture-resistant MDF), it stands out in several ways:
- Plywood: Plywood is made by layering thin sheets of wood veneer, with the grain of each layer running perpendicular to the next. It offers superior strength and stiffness compared to MDF but is more expensive and has a visible wood grain pattern. Check out our in-depth comparison of Plywood vs MDF here.
- Particleboard: Like MDF, particleboard is an engineered wood product made from wood particles. However, it uses larger wood chips and has a lower density, making it less durable and more prone to swelling and delamination.
- Solid Wood: Natural solid wood panels, like those made from oak or maple, offer unmatched strength and aesthetic appeal. However, they are significantly more expensive than MDF and can be prone to warping, cracking, and other defects.
Painting MDF
One of the advantages of MDF is its smooth, uniform surface that readily accepts paint and other finishes. However, there are a few important considerations when painting MDF:
- Surface Preparation: MDF should be lightly sanded and cleaned to remove any debris or loose fibres before painting. This helps the paint adhere properly.
- Primer: Using a quality primer designed for MDF is essential to seal the surface and prevent excessive absorption of the topcoat, which can lead to a blotchy finish.
- Paint Type: Water-based acrylic paints are generally recommended for MDF as they don't react with the wood fibres as strongly as some oil-based paints.
- Edge Sealing: The edges of MDF panels should be sealed with a suitable edge banding or sealant to prevent moisture absorption and potential swelling or delamination.
For a more detailed guide on painting MDF, including recommended products and techniques, visit our Painting MDF article.
Cutting MDF
Another great advantage of MDF is its workability - it cuts cleanly and easily with standard woodworking tools. Here some tips to follow for best results when cutting MDF:
- Saw Blades: Use saw blades designed for cutting composite wood products like MDF or melamine. These have more teeth designed to prevent chip-out and achieve a smoother cut.
- Scoring: For handsaws or circular saws, scoring the cut line first can help prevent edge chipping and blowout on the bottom face.
- Blade Height: Adjust the blade height on saws so it only extends slightly below the MDF thickness to minimize tearout.
- Feed Rate: Take slower, steady passes rather than aggressive force-feeding to avoid chipping and rough edges.
- Dust Collection: MDF produces extremely fine dust when cut, so always use proper dust extraction or work outdoors to avoid breathing in particles.
- Support: Providing adequate support underneath longer MDF panels when cutting can prevent sagging and inaccurate cuts.
For a more in-depth guide on cutting MDF cleanly and safely with various saws, routers, and other tools, check out our Cutting MDF article.
Our Range of Cut-To-Size MDF
Looking for quality MDF sheets for your next project? Cut My has a wide range of cut-to-size MDF boards available to order online with fast delivery across the UK. From standard, moisture-resistant, and fire-resistant fiberboard, to decorative melamine MDF - we've got you covered. Our large stock and efficient order fulfillment ensure you can get the MDF you need, when you need it.