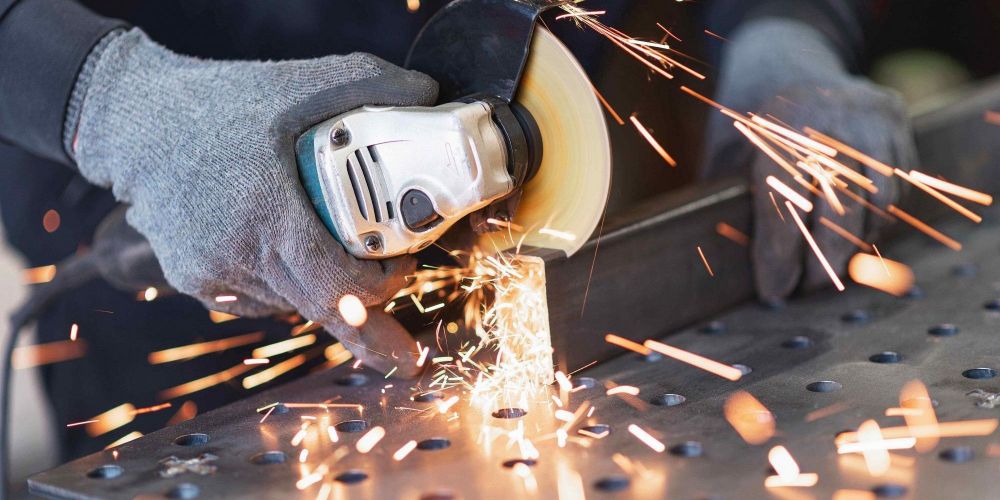
As a do-it-yourself enthusiast, you may find yourself in need of cutting metal for a home project. An angle grinder can be an extremely useful tool for cutting metal, allowing you to complete the task with relative ease. Before you start slicing through sheets of metal, it is important to understand how to properly and safely operate an angle grinder.
What Angle Grinder and Cutting Disc do I need?
Choosing the proper cutting disc and angle grinder is essential for successful metal cutting. For most metals, a diamond-cutting disc is ideal as it can cut through hard and soft metals. As discs dull over time with use, they become less effective and more difficult to control.
Selecting an Angle Grinder
For metal cutting, choose an angle grinder with a motor that draws between 5 to 9 amps for small cuts on thin sheet metals, or 9 amps or more for cutting thicker, denser metals. Higher amperage means more power and faster cutting. Other features to consider include a spindle lock for quick disc changes, as well as a guard to protect you from flying debris.
Choosing Cutting Discs
Profile
Two common profiles of cutting discs are Type 41 and Type 27.
Type 41 cutting discs, also known as flat cutting discs, are primarily designed for cutting thin materials. These discs have a flat profile with a slight depression around the centre. They are ideal for tasks that require precision and finesse.
Type 27 cutting discs, also known as depressed centre cutting discs, are designed for heavier-duty tasks. These discs have a raised hub, allowing for aggressive cutting and grinding.
Material Types
There are several grain types of discs specially designed for cutting various metals using an angle grinder. Choosing the correct disc ensures efficient, safe cuts and reduces wear on the grinder.
Abrasive Cutting Discs
The most common angle grinder discs are abrasive discs made with either aluminium oxide or silicon carbide grains. These abrasive discs are suitable for cutting mild steel, stainless steel, iron and other ferrous metals. For thicker metal, use a coarse grit disc. Finer grit abrasive discs produce smoother edges. Abrasive discs wear at a steady rate during use.
Diamond Cutting Discs
Diamond discs contain industrial-grade diamond particles that provide super hard cutting edges. Diamond discs maintain their cutting sharpness longer than other abrasive discs. They are ideal for stainless steel, chrome, titanium, ceramic tile and glass. Diamond discs quickly cut through hard, dense materials with minimal wear during use.
Carbide Cutting Discs
Carbide discs have teeth made of tungsten carbide brazed on a steel core. Carbide teeth are extremely hard for aggressive cutting. The jagged teeth chip away material as the disc spins. Carbide discs work well for cutting steel angle iron, steel sheet, rebar, wire and pipe. They handle thick, hard metal but do wear over time.
Stainless Steel Cutting Discs
Stainless steel cutting discs are made using compressed stainless steel abrasive grains. They cut efficiently through tough stainless steel and nickel alloys. Stainless discs resist material loading while cutting which can slow other abrasive discs. This makes them last longer when cutting stainless steel.
Aluminium Oxide Flap Discs
Flap discs have overlapping abrasive flaps that cut aggressively through metal. The flaps quickly clear away the material being cut. Flap discs with aluminium oxide abrasive are good for cutting stainless steel, mild steel and other alloys. Flap discs produce clean, smooth cuts in metal.
Thickness
For cutting thick metal, choose an appropriately thick cutting disc. Thinner discs are prone to breaking when used on thick materials. The rule of thumb is to use a cutting disc thickness that matches the thickness of the metal stock.
For precision cutting, 1.0mm - 1.6mm discs are ideal, especially when working with thin materials like mild steel and aluminium. These thicknesses are perfect for fabrication, welding preparation, and detailed metalwork.
For heavy-duty cutting and grinding, opt for 2.0mm - 3.0mm discs, especially when dealing with tougher materials such as stainless steel and cast iron. These offer stability and durability for construction and industrial applications.
Cutting Techniques
To cut metal accurately and efficiently with an angle grinder, it is important to understand proper techniques and safety precautions. When cutting metal, always wear appropriate safety gear like work gloves, protective eyewear, and sturdy footwear.
Straight cuts
For straight cuts, carefully mark the line you wish to cut on the metal surface. Secure the metal in place, either in a vice or clamp. Align the cutting disc on your marked line and slowly cut through the metal using light pressure. For longer, straighter cuts, use a clamped straightedge as a guide. Score the line first by lightly running the disc along the cut line. This will help guide your cut and prevent the disc from slipping. Move the grinder smoothly along the line at an even speed.
Curved cuts
To cut curves, mark the desired curved line on your metal piece. Carefully cut along the line with multiple passes of the grinder, removing small amounts of material with each pass. For tight curves, a cutting disc with a smaller diameter may provide more control and accuracy. Go slowly, checking your progress frequently.
Holes
Angle grinders can also be used to cut holes in metal. Mark the desired hole size on the metal. Carefully plunge the cutting disc into the metal at an angle and move the grinder in a circle to cut the hole. For larger holes, start by drilling pilot holes, then use the cutting disc to connect the holes. Be very careful when cutting holes, as the metal piece may become unstable. Secure the metal or have an assistant help support it.
Common Mistakes When Cutting Metal With an Angle Grinder
When using an angle grinder to cut metal, there are a few common mistakes you'll want to avoid. Following proper safety precautions and techniques will help you get clean, accurate cuts.
Choosing the Wrong Disc
Selecting an incorrect cutting disc can lead to poor cut quality, increased risk of kickback, and disc damage. Choose a disc specifically meant for cutting metal that matches the thickness and type of metal you're cutting.
Applying Too Much Pressure
Applying too much pressure when cutting can cause the disc to bind, kick back, or break. Let the speed and abrasiveness of the disc do the work. Apply light, even pressure and move the grinder smoothly along your cut line.
Incorrect Cutting Angle
Holding the grinder at the wrong angle can lead to an uneven, jagged cut. For straight cuts, hold the grinder at a 90° angle to the workpiece. For bevelled or angled cuts, hold the grinder at the desired angle and move it steadily to achieve a smooth cut.
Inappropriate Workpiece Clamping
If the workpiece is not securely clamped in place, it can shift during cutting and cause injuries or an uneven cut. Clamp the workpiece to a stable work surface to keep it stationary. For small pieces, use locking pliers or a vice to grip the workpiece.