Acrylic is a versatile and widely used material, particularly beloved by DIY enthusiasts for its wide range of applications and impressive properties. This article will provide a detailed look into how acrylic is made, helping you understand its manufacturing process, various forms, properties, and numerous applications.
What is Acrylic?
Acrylic, often referred to as acrylic plastic, is a type of synthetic polymer derived from acrylic acid. Known for its optical clarity, excellent resistance to UV light, and high impact resistance, acrylic is a popular choice across various industries. It was first developed in the early 20th century and has since become a staple in the production of items ranging from household goods to industrial applications. The material’s clarity rivals that of glass, but it offers superior impact resistance and is lighter, making it a practical alternative for many uses.
Types of Acrylic Plastic
Acrylic plastics come in several forms, with polymethyl methacrylate (PMMA) being the most common. There are two primary types of acrylic sheet: cast acrylic and extruded acrylic. Cast acrylic is produced by pouring liquid acrylic into moulds, which allows for the creation of thicker sheets and provides superior optical clarity. This method is more labor-intensive but results in high-quality material suitable for applications where appearance is critical.
Extruded acrylic is made by pushing acrylic through a die using a continuous method. This process is more cost-effective, suitable for mass production, and ideal for applications where thinner thicknesses and smaller widths are needed.
Both types of acrylic have their unique advantages, making them suitable for different uses depending on the specific requirements of a project.
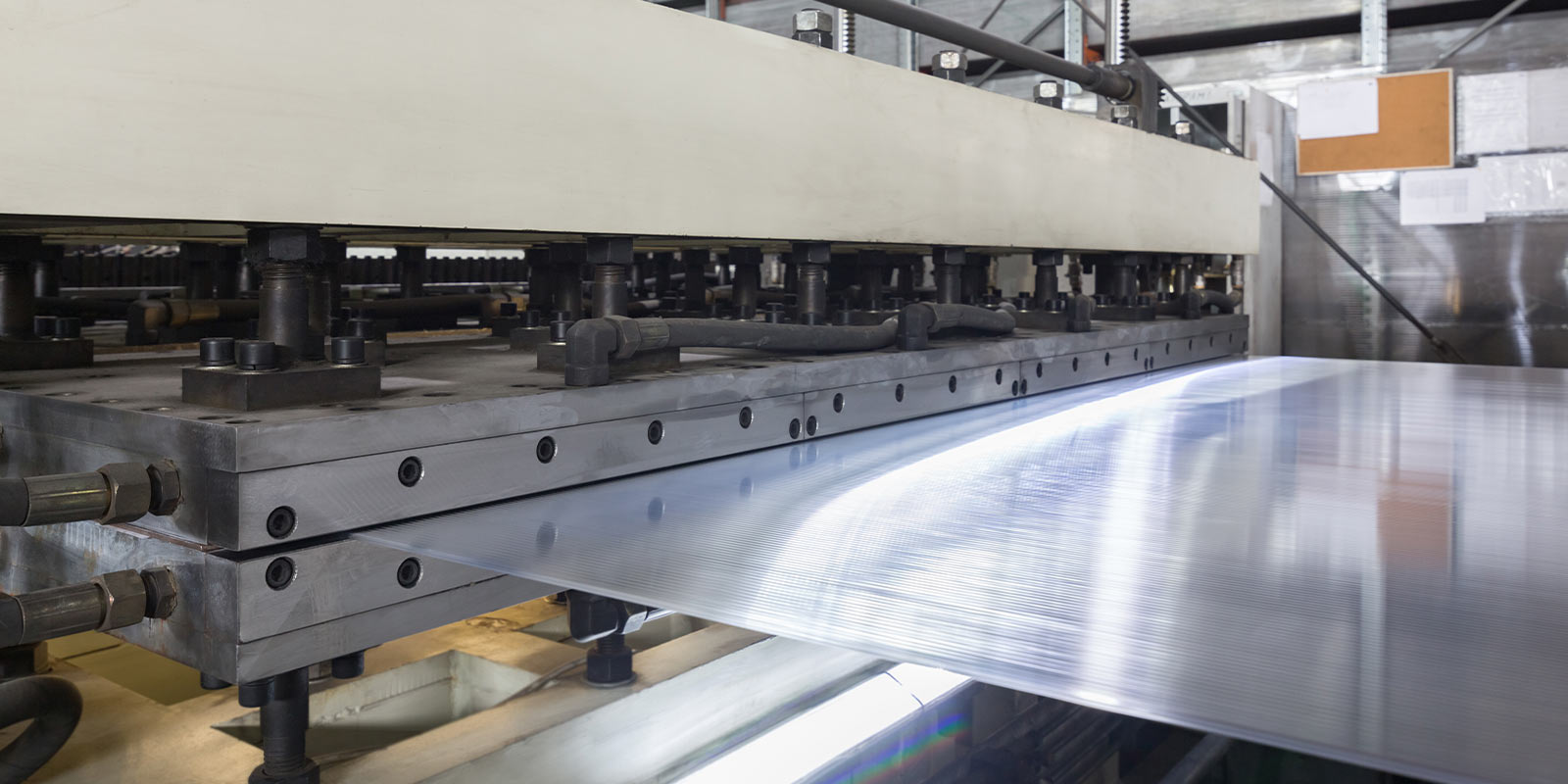
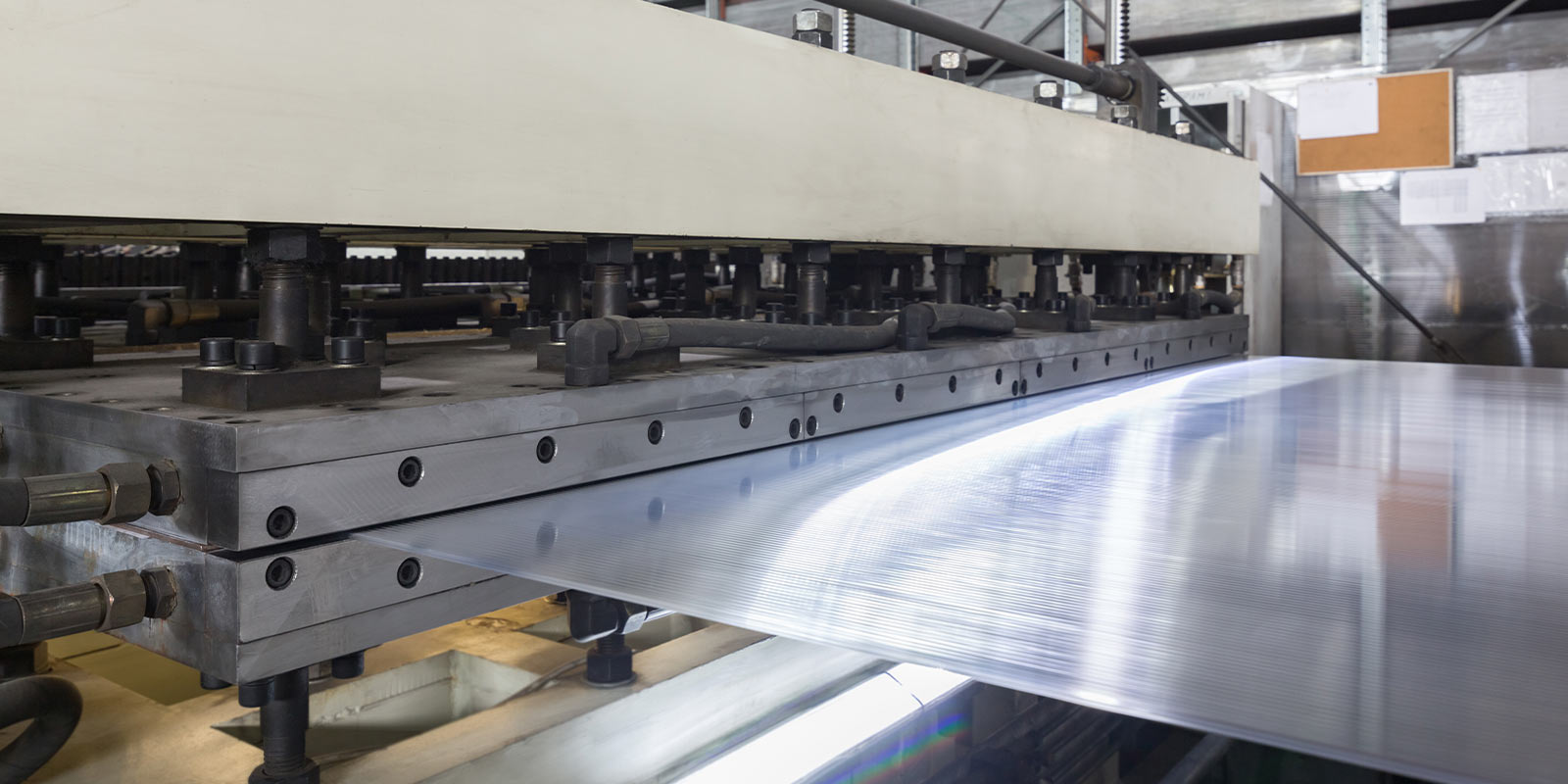
Raw Materials Used in Acrylic Production
The production of acrylic begins with raw materials such as methyl methacrylate (MMA), acetone, and sodium cyanide. These chemicals undergo various chemical reactions to form the base monomer, which is then polymerized into acrylic.
Methyl methacrylate is the primary building block, providing the necessary properties for the final product. Acetone and sodium cyanide play crucial roles in the synthesis process, helping to initiate and control the polymerization reactions.
The quality and purity of these raw materials are essential for producing high-quality acrylic with the desired properties.
How Acrylic is Made
Polymerization
The first step in making acrylic is polymerization, where methyl methacrylate is mixed with a catalyst in a controlled environment. This chemical reaction causes the monomers to link together, forming long polymer chains.
The polymerization process can be performed in batch cell reactors for smaller production volumes or continuous bulk polymerization for large-scale manufacturing.
The choice of method depends on the desired production scale and the specific requirements of the acrylic being produced.
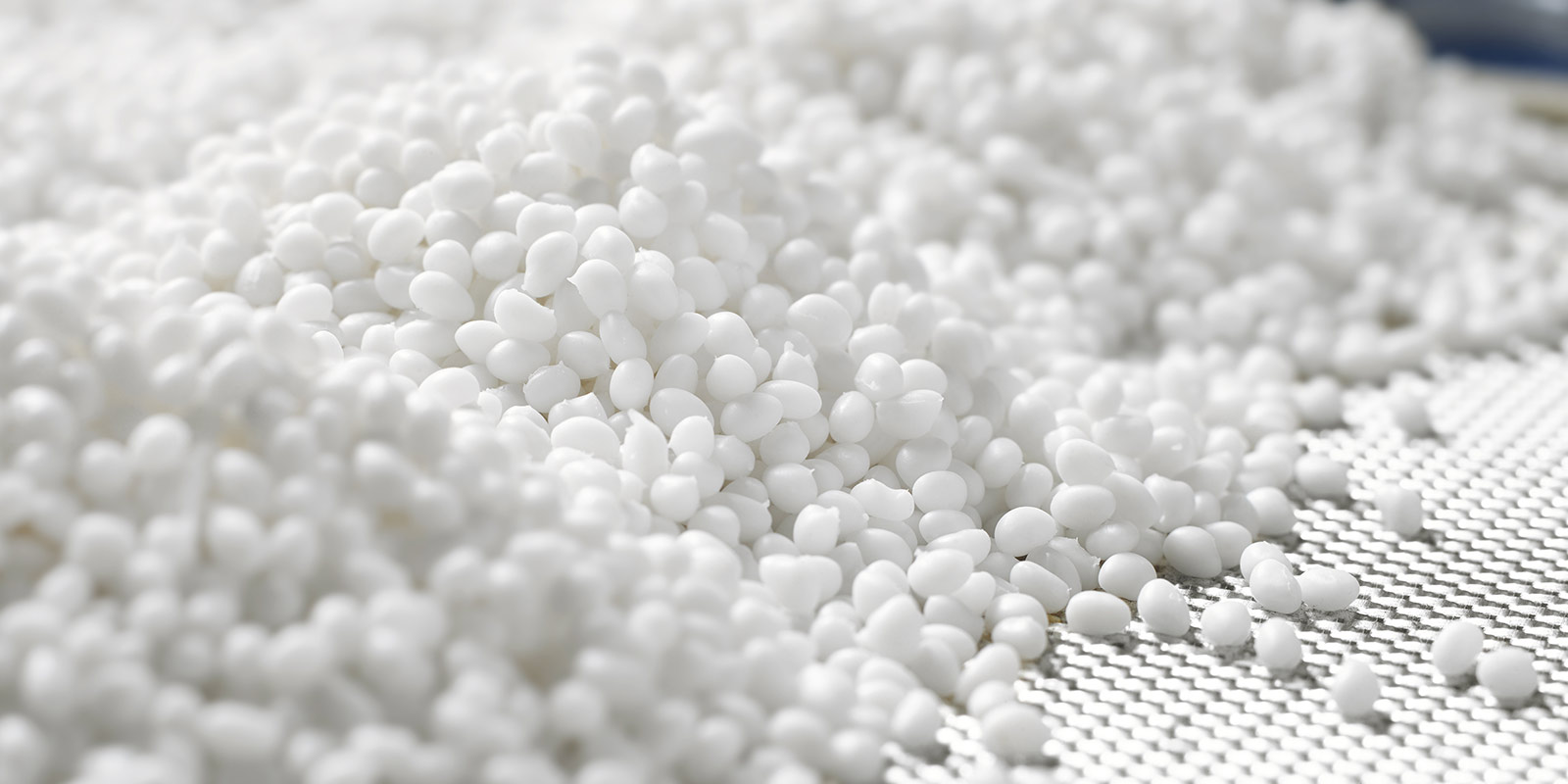
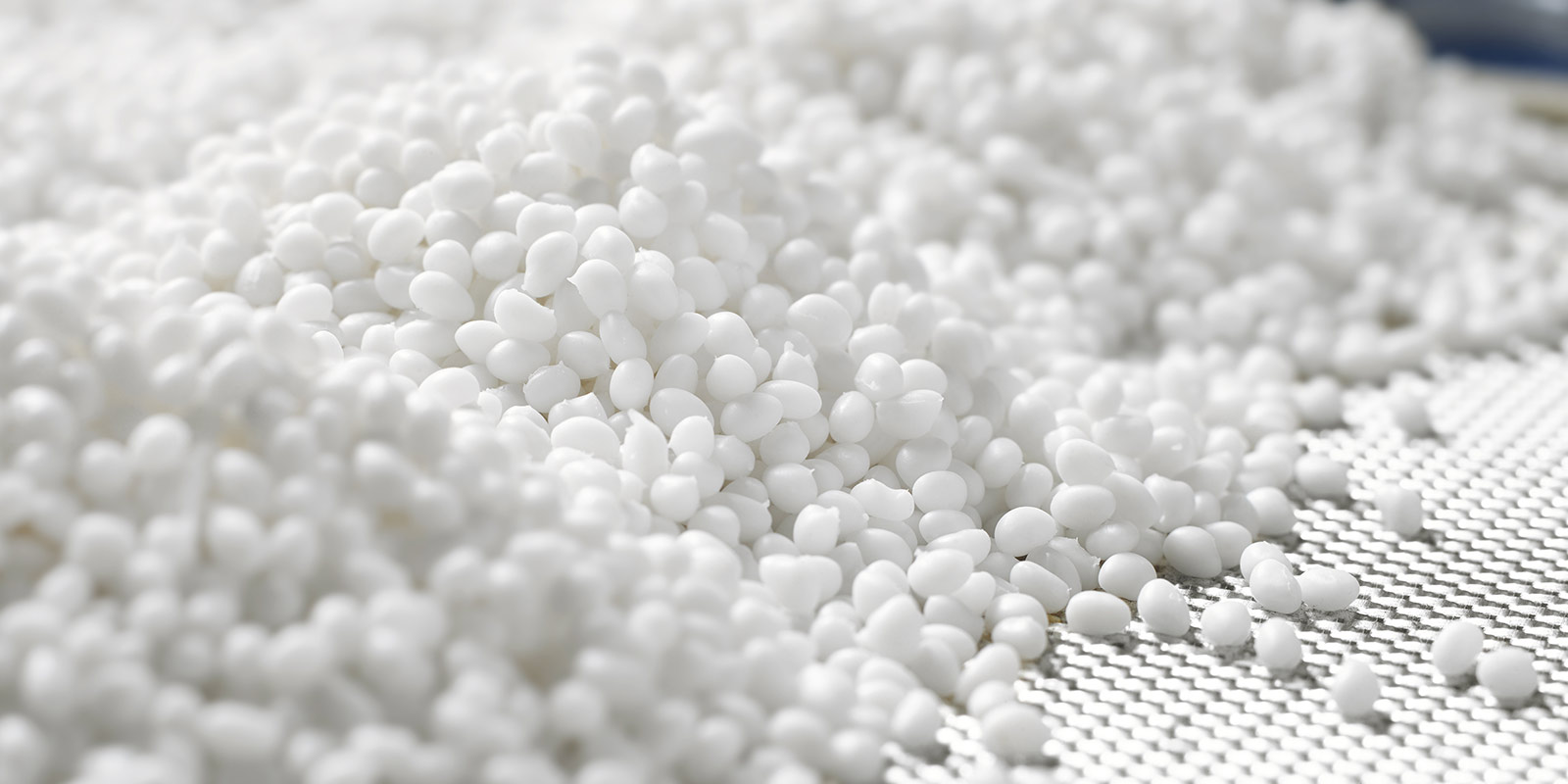
Casting or Extrusion
Once the polymerization is complete, the polymerized acrylic can be formed into sheets through either casting or extrusion. In the casting process, the liquid acrylic is poured into moulds to form flat sheets. This method allows for the production of thicker sheets with superior optical clarity. Cast acrylic is highly valued for its visual quality and is often used in applications where appearance is paramount, such as retail displays, high-end furniture, and decorative items.
The extrusion process involves pushing the polymerized acrylic through a die, producing continuous flat sheets. Extruded acrylic is more cost-effective and suitable for applications requiring smaller widths and thinner thicknesses, such as signage, glazing, and protective barriers.
Curing and Cooling Acrylic Sheets
After the acrylic sheets are formed, they undergo curing to solidify the material. This step involves heating the acrylic to remove any residual chemicals and achieve the desired hardness.
Curing is a critical process, as it ensures the acrylic attains its full strength and durability. Following curing, the acrylic must be carefully cooled to prevent contamination and maintain the sheets' high clarity and impact resistance.
The cooling process must be precisely controlled to avoid introducing stresses or defects that could compromise the material's performance.
Quality Control and Finishing
Quality control is crucial in the manufacturing process to ensure the final product meets industry standards. This includes inspecting the sheets for optical clarity, thickness uniformity, and the absence of impurities.
Advanced testing methods, such as optical inspections and mechanical testing, are used to verify that the acrylic meets the required specifications. Finishing techniques such as polishing, cutting, and laser cutting are employed to achieve the desired dimensions and surface quality.
Polishing removes surface imperfections and enhances the material's clarity, while cutting and laser cutting allow for precise shaping and customization.
Multiple pieces of acrylic can be bonded together using specialized adhesives for more complex projects, enabling the creation of intricate designs and assemblies.
Environmental Considerations
The production process of acrylic does have environmental impacts, primarily due to the chemicals involved. However, advances in eco-friendly manufacturing practices are being made, such as recycling acrylic plastics and reducing emissions.
Many manufacturers are exploring ways to minimize waste and improve the sustainability of acrylic production. For example, scrap acrylic from the manufacturing process can be recycled and reprocessed into new products.
Additionally, efforts to reduce the use of harmful chemicals and improve energy efficiency are ongoing. Acrylic's durability and long lifespan also contribute to its sustainability by reducing the need for frequent replacements, which can help lower overall resource consumption.
Applications of Acrylic
Acrylic plastic is used in various applications due to its excellent resistance to impact and UV light. It is commonly used for outdoor signs, display cases, brochure holders, and retail displays. These applications benefit from acrylic's clarity, weather resistance, and ease of fabrication.
In the medical field, acrylic is used for making medical devices due to its clarity and sterilizability. It can be easily moulded into precise shapes, making it ideal for custom medical equipment and protective barriers.
DIY enthusiasts often use acrylic for projects like furniture, aquariums, and decorative items because of its versatility and ease of fabrication. Acrylic's ability to be cut, shaped, and bonded allows for endless creative possibilities, from simple frames and enclosures to complex multi-piece assemblies.
Tips for DIYers Using Acrylic
For DIY enthusiasts, working with acrylic plastic sheets can be highly rewarding. Here are some tips to help you get the best results:
- Cutting and Shaping: Use tools like saws or laser cutting machines for precise cuts. Ensure the tools are sharp to avoid cracking. Laser cutting is particularly effective for achieving clean, intricate designs, while saws are suitable for straight cuts and larger pieces.
- Joining: Plastic material can be bonded using specialized adhesives. Clean the surfaces thoroughly before joining to ensure a strong bond. Proper surface preparation is essential for achieving a durable, clear joint.
- Safety: Always work in a well-ventilated area to avoid inhaling fumes. Wear protective gear, including gloves and goggles, to protect yourself from sharp edges and chemical exposure.
- Maintenance: Clean acrylic plastic with a mild soap solution and a soft cloth. Avoid abrasive cleaners that can scratch the surface. Regular cleaning helps maintain the material's clarity and appearance.
- Storage: Store acrylic sheets in a cool, dry place to prevent warping or discolouration. Keep the sheets flat and avoid stacking heavy objects on top of them to maintain their shape and quality.
Conclusion
Understanding how acrylic plastic is made helps DIY enthusiasts choose the right materials for their projects and achieve professional results. Acrylic's versatile properties, such as high impact resistance, optical clarity, and ease of fabrication, make it a popular choice for various applications.
Whether you're making outdoor signs, display cases, or custom furniture, knowing the ins and outs of acrylic manufacturing can elevate your DIY projects to the next level. With its combination of durability, aesthetics, and workability, acrylic is an ideal material for a wide range of creative and practical uses.
Additional Resources
For those interested in further exploring acrylic materials, here are some useful resources:
- Suppliers of Acrylic Sheets in the UK: Local suppliers can provide various acrylic sheets suitable for your projects. Researching and connecting with reliable suppliers can ensure you get high-quality materials for your needs.
- Tutorials on Working with Acrylic: Online tutorials can offer step-by-step guidance on cutting, shaping, and joining acrylic. These resources can help you master the techniques needed to work with plastic materials effectively and safely.
- Recommended Reading: Books and articles on acrylic plastic fabrication techniques and project ideas. Expanding your knowledge through reading can inspire new project ideas and improve your skills.
Share Your Acrylic DIY Projects
We invite you to share your acrylic plastic DIY projects and experiences with our community. Sign up for our newsletter for more tips, guides, and inspiration.
Follow us on social media @cutmy.uk to stay updated with the latest trends in DIY projects using acrylic materials.
By understanding the detailed process of how acrylic is made, DIY enthusiasts can better appreciate this versatile material and its wide range of applications.
Whether you're crafting custom retail displays, medical devices, or unique home decor, acrylic offers endless possibilities for creativity and innovation.
Join our community to learn more and share your own creative projects with others.